The easiest way to recognize a dust control program that is working is to simply not see any more fugitive, respirable mine dust. Sometimes, achieving this while avoiding a host of other negative side effects is difficult, especially when using above-ground surface dust control methods.
But for one current client of Midwest’s, this is exactly what they are experiencing.
This client, an underground hard rock mine, had tried everything. Their most common approach was watering: they relied on daily applications of water to attempt to suppress their respirable mine dust. This meant watering trucks moving through tunnels and roadways almost constantly.
Our contact at the mine had expressed frustration with watering as well as an endless list of methods and products he had tried, because all of these approaches were causing damage to equipment.
According to him, “…watering created an awful environment to work in. It turned everything to mud, which got into the equipment and made walking through the tunnels a nightmare.” Lignosulfonates also created that “black sticky” problem, causing tar-like stains on equipment that required additional time and money to clean.
The mine came to Midwest to help them implement a more efficient respirable mine dust control program that would help them achieve their dust suppression objectives while eliminating both watering and grading. Using the MineKleen™ Program, we set up two tests for them to determine the most effective way to address their respirable mine dust challenges.
They were blown away by the results.
The Test: achieving respirable mine dust control
To set up these tests, we identified two areas, one that was low-traffic and had a high level of ventilation and one that was high-traffic but with lower ventilation.
Understanding ventilation is important to controlling respirable dust in underground mines, because these facilities face very different environmental conditions from above-ground roadways. Many mines treat their tunnels and other underground spaces like they do their above-ground haul roads and tailing sites, but this approach doesn’t make sense.
Above-ground areas face varying temperatures and weather patterns. Dust can shift from untreated areas to treated areas due to wind movement, spillage and track-on. Wind and rain can temporarily clear dust. And while traffic does stir up dust, that fugitive dust doesn’t get caught in a cycle.
Underground areas are rarely affected by these factors. There is no variable weather, wind speed is fairly constant based on the ventilation systems and traffic patterns are fairly set. Instead, they encounter these challenges:
- The same dust is always recirculated and suspended in the air because of the ventilation systems. These systems serve to both recirculate current respirable mine dust and new dust introduced from various sources.
- Traffic causes dust particles to fly off the roads and onto ribs, which results in the dust recirculating in the air.
These factors create a perfect storm scenario, where dust has nowhere to go but to stay suspended in the air, creating respiratory mine dust problems for crews, clogging up equipment and restricting productivity.
For this particular mine, our application technicians found two different areas and developed two separate treatment cycles. One treatment plan, for the low-traffic, high ventilation area, was prescribed a six-week application span. The other treatment plan, for the high-traffic, lower ventilation area, was assigned a two-week application rate.
Both have worked remarkably well. Both watering and grading have been eliminated after only ten weeks. Observable and analogical improvements include far less dust in the air, dry conditions, cleaner equipment and less use of equipment to control the respirable mine dust. Meanwhile, because MineKleen is so neat, there’s no more wet, muddy, sticky conditions in the tunnels. Equipment and clothes stay dry and equipment and mine professionals do not need to trek through the mud.
Above all, though, our contact was impressed by the visible difference: two weeks after the initial treatment of our product, MineKleen Plus®, he told us “We can literally SEE the difference. If I had to guess, we’re getting a good 90% dust control 10 days after our initial application.”
The Results: it’s about the program, not the product
Getting these results requires a scientific approach to respirable dust control, as outlined above. From initial data gathering to custom planning for different locations with unique characteristics, Midwest’s focus on optimizing dust suppression programs to fit your underground mine’s specific needs sets us apart.
Midwest focuses on creating an entire program — called MineKleen Underground Mine Dust Control — that emphasizes the importance of application over product. While product chemistry is certainly important (our product chemistries are the most sophisticated and environmentally friendly on the market), decades of experience have taught us that how any given product is applied makes up 60% of the possible results you can expect. And we custom built the application equipment so your team can typically apply the product in a single pass (all road and rib surfaces).
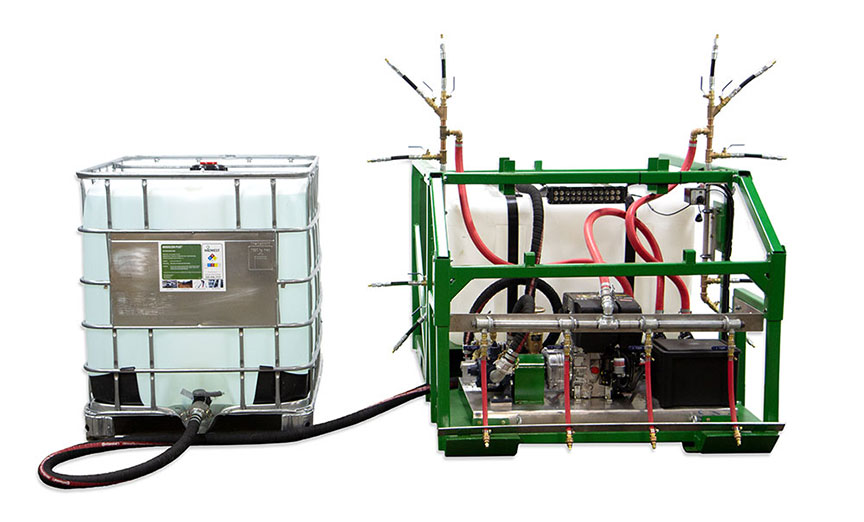
This is why we track from start to finish; why we test, then tweak, before rolling out an entire program; why we get to know you and your mine. This allows our technicians and chemists to make the best recommendations to accomplish your goals, while minimizing your dust control budget. If respirable mine dust has you in a cloud, clear things up by implementing a test with Midwest. We have dust control down to a science, and that includes a specific product, equipment and dust suppression program specific to underground mines: MineKleen Underground Dust Control.