You know that your gravel runway maintenance costs are getting away from you. Every time a plane takes off or lands, you literally watch a small part of the surface fly away. You’re out there grading it weekly, trying to minimize the impact. And you know that eventually you’ll have to replace it.
But do you know what your gravel runway maintenance costs really are?
The Impact of Reactionary Gravel Runway Maintenance on Costs
The dust that lifts up during landing or take-off contains both gravel and fines (the particulate matter that holds your runway together). This means that a shifting runway is a compounding problem: the more material that moves, the more prone the surface is to lose more material.
Every take-off or landing moves between 2.5 to 5 cubic meters of gravel. Combined with the loss of fines, this contributes to potholes and rutting. It also leads to an overall softer surface. Regular grading can help with this, but it also increases your gravel runway maintenance costs.
Should you, for any reason, fail to keep your runway perfectly maintained, the risk and associated costs can quickly get out of hand.
FOD (foreign object debris) can cause physical damage to a plane’s exterior or even engine. (Like the wing damage in the picture below.)
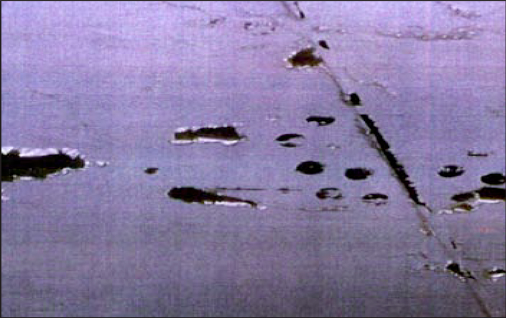
Loose surface material or a failure of surface strength can cause a plane’s tire to literally sink into the runway, trapping it.
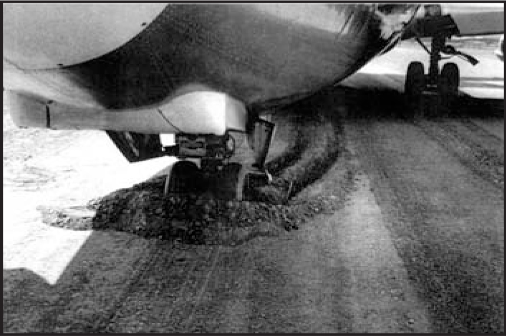
And, of course, extensive dust in the air can blind pilots, increasing the risk of crashes.
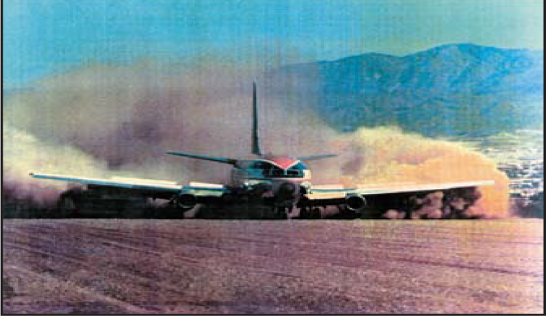
Should damage occur to aircraft, airlines can pass the costs associated with repairs back to you, adding on to your gravel runway maintenance costs. These can easily run into the tens or hundreds of thousands of dollars.
Additionally, softer surfaces mean that heavier planes need longer runways. If you rely on a gravel landing strip for either bringing in supplies vital to your community or hauling out a shipment of cargo, keeping large shipments together makes a big difference for cost control. Breaking those shipments down to accommodate smaller planes will also add to your gravel runway maintenance costs.
Finally, the costs and risks associated with a poorly maintained runway go beyond airlines or economics. The dust produced by constant traffic on a gravel runway has been demonstrated to negatively affect both the local community and local environment.
Many rural Alaskan communities, for example, spend their summers plagued by overwhelming dust. And it’s not only an irritant; it also plays a role in increasing symptoms of asthma and other health issues to do with the lungs.
Standard Gravel Runway Maintenance Costs – Why Water Costs You More
Many owners and operators of unpaved airstrips limit maintenance to regular application of water to mitigate dust and grading or spot fills to replace lost gravel and fines.
Using water for dust management is counterproductive. It only works for its intended purpose from a few hours to a couple of days at a time. Meanwhile, it erodes your surface, causing it to break down and soften. This naturally increases the amount of time (and money) you have to dedicate to grading.
Grading does help somewhat, but when you start to add up the cost of running your grading equipment as often as it’s needed, it starts to add a lot to your gravel runway maintenance costs.
Meanwhile, maintaining your gravel runway also requires frequent inspections and testing. Did you know that there’s a minimum recommendation for testing? It’s every three years, after any new construction, after a single season of disuse, or when there is a suspected degradation of surface shear strength (e.g., a pilot complains about your runway surface being too rough).
Ultimately, the impact of any measures that are not proactive is that, like most gravel runways, yours will have to be rebuilt entirely every ten years.
When you add it all together, from regular maintenance and testing to complete rebuilds, some estimates put gravel runway maintenance costs at almost $2.5 million over 20 years, or $122K per year.
Save $215,900 in Costs, and Get a More Durable Runway, with Midwest’s Semi-Permanent Dust Control Solution
It is possible to cut temporary water and its associated costs significantly. A more proactive, preventative approach is to use Midwest’s semi-permanent dust control system that combines soil chemistry with synthetic polymers to bind soil particles together, reducing maintenance events.
There are two important components of Midwest’s semi-permanent solution. First, of course, is the product itself. You can use products that lack a binder, meaning they won’t work as effectively or for nearly as long. Or, you can pay a bit more upfront to get one that will preserve your gravel runway long enough that you can actually shift your rebuild cycle. This would have a huge impact on your average gravel runway maintenance costs.
The other component is the application. The best product on the market, if installed by the wrong people, will ruin your runway. You need experienced dust-control specialists who know how to get the most out of your product. And who responsibly monitor, manage and measure results.
To see how this can impact your operation, let’s take a look at the numbers in action. (Data comes from experience with and projections by Midwest Industrial’s customers.)
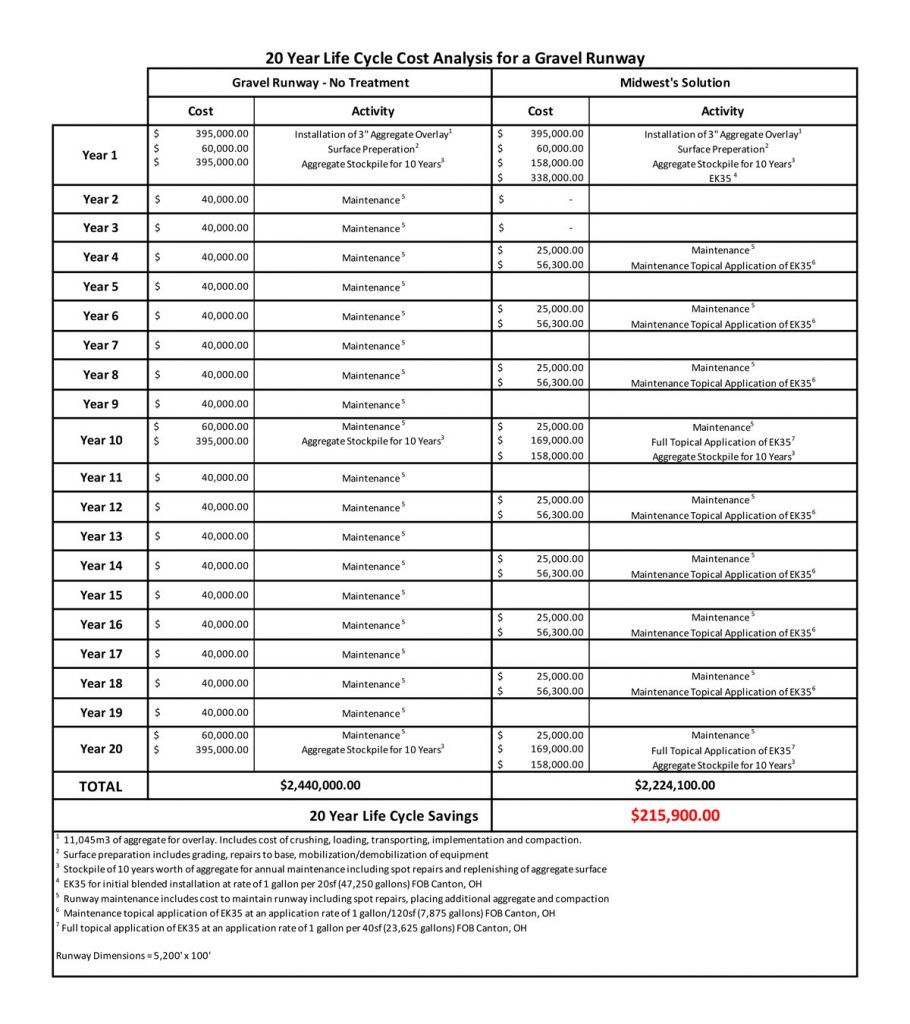
The total cost savings over 20 years is $215,900, or $10,795 a year.
(Note: these estimates are extremely conservative and may very well be higher in your individual context. Contact Midwest for an estimate based on your specific requirements and location.)
But the benefits go beyond mere direct cost savings. You’ll need less maintenance, and therefore less opportunity cost from using labor and equipment for watering programs that you could use elsewhere.
You’ll have a better performing, safer and more reliable runway. And less wear and tear to aircraft due to degrading runway surfaces.
Imagine not having to do weekly grading. Or regular watering or inspecting. And no complaints from pilots about rough landings. Meanwhile, you could save nearly a quarter million dollars over the next 20 years, while having a gravel runway that stays in excellent condition.
To learn more about how Midwest can lengthen the lifecycle of your gravel runway and get your gravel runway maintenance costs under control, visit our Gravel Runway program page.