For those who know Midwest, it’s no mystery that we believe dust mitigation can be managed — scientifically — to achieve predictable results. Predictable results equal predictable budgeting, reliable safety and compliance, and achievable metrics. That happens because we focus on the program as much as the product. The product is a part of the whole effort to control dust at your site, which begins with collecting data and ends with demonstrating objectives that have been successfully met. We call it Dust Control Down to a Science.
This is exactly how we approached the challenges faced by one recent client, a large industrial facility.
This facility was struggling to mitigate dust in 15 different areas, both roads and open spaces, around their site. This made compliance with local regulations, which required fugitive emissions levels to remain below a level of 15% instantaneous opacity, difficult.
They brought us on board to implement an Emission Reduction Program (ERP) within the context of our Turnkey Managed Services Program.
For those who may be unfamiliar, the goal of an Emission Reduction Program is to establish an ongoing work practice standard that sufficiently mitigates fugitive emissions, while utilizing the least amount of dust suppressant chemical possible. The value of this is a program that is customized to each unique site. No site is the same. There are different climates, traffic volumes, soil types, required objectives and more, all of which impact how successful any attempt at dust mitigation will be.
By optimizing our approach to each site, we can match the right amount of product to meet exact needs; no guessing or wasted spend required.
After collaborating with a given client to understand their needs and goals, each program begins with data collection. Traffic flows and loading, spillage, track-on and contamination sources, soil type, product chemistry, industrial attributes and more all factor into our technicians’ process for determining how much product is needed, at what volume and application rate, to achieve the desired goals.
In the case of this customer industrial facility, we used silt load testing and instantaneous visual emission observations (IVEOs) for opacity (by certified observers) to determine pre-control dust levels and to provide credible evidence of fugitive emission control.
These tests revealed a pre-season silt level for untreated surfaces of 801.36 g/m2 (grams per square meter). The pre-season instantaneous opacity was 25%.
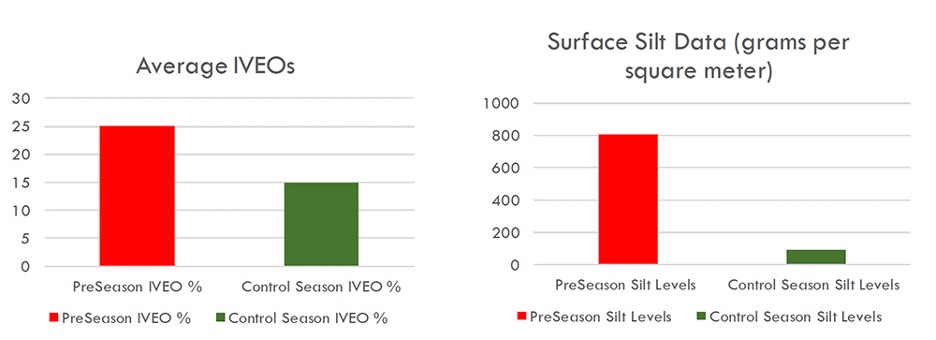
On-target dust mitigation
Implementing our Managed Services Program involved having dedicated Midwest staff onsite for observation, data gathering and dust suppressant application.
We applied EnviroKleen, our leading dust mitigation product, to roadways and open areas during the control season. EnviroKleen is a synthetic fluid with a binder. It works by tying dust particles together in a network that keeps them bound to each other and larger aggregate, holding them in place. Unlike many other off-the-shelf dust mitigation products, its binding properties allow the road surface to get stronger with usage, meaning less product is needed for future maintenance applications. This allows EnviroKleen to actually strengthen the road surface as well as fugitive dust.
The initial application and subsequent maintenance applications brought emissions to within established guidelines for the period, through to the end of the control season. For Instantaneous Visual Emission Observations (IVEOs), this was a reduction from 25% to 15%, which was in compliance with local regulations. For silt loads, levels were under 100 g/m2, which was a 90% reduction in levels since the pre-season measurements.
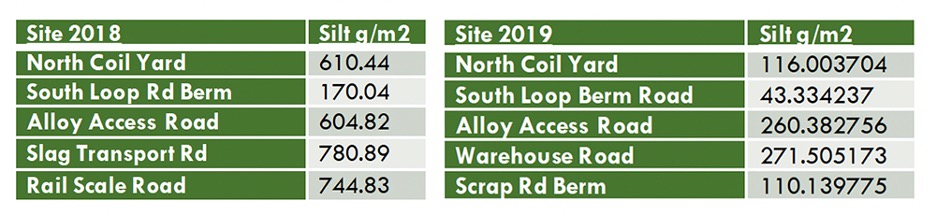
As an example of how unique conditions can adversely affect dust mitigation efforts, one of the 15 areas where EnviroKleen was applied showed fluctuating silt levels throughout the season. The specific factors impacting this area included surface grading activity and adjacent roadway construction/repair, activities that can kick up excessive dust that drifts onto treated areas. To resolve this in the next season, we recommended that the facility coordinate repairs and grading to minimize their impact on dust mitigation efforts.
Start with goals, end with results
At Midwest, we always begin with the end in mind. This means understanding exactly what you need to accomplish. We will never sell you a product without understanding what you need it to do. The advantage of this is efficiency: you don’t waste money buying a product that can’t deliver what you need, nor do you waste money by paying for more results than you need.
Once we understand your target metrics, we can build a custom plan to hit those metrics. We can run a trial on your site first, giving you the chance to see our program in action before rolling it out to your entire facility. This will give you predictability: in your budget, in your future planning and in the success of the program.
If you believe a trial would be valuable for your site, learn more about our dust mitigation program and contact us for a complete analysis.