We’ve talked a lot about the science of dust control—such as the many factors that affect your dust control program—here on our blog. As we’ve said many times, dust control in mining is never as simple as dumping water on an unpaved haul road and hoping that cuts it. Instead, as an operations manager at a mine, you have to take into consideration a range of issues, from your production schedule to local climate to road base quality and more.
With Midwest’s experience, we can come in as an advisor to collect and weigh all these factors for you, bringing you clarity on the best option for your mine, to effectively control dust in the most economical way possible.
Which brings us to today’s article: a case study for one Peruvian mine where we did exactly this.
We conducted a test on a 750 meter long stretch of haul road that led to a dump site. The entire surface area to be covered was 22,500 square meters (the road was 30 meters wide). To accomplish this test, we provided the mine with just over 35,000 liters of our leading dust control product, EK35B, along with loaning them one of our e-sprayers for easy application. Trained site personnel from the mine performed the application with oversight from Midwest. The trial lasted 45 days, during which time the EK35 was applied 17 times (with an additional application on a curve; see more below).
Site background – successfully planning a program for dust control in mining
Going into this project, we knew that we would be facing ideal weather for heavy dust. The local climate was extremely arid, with an average annual temperature of 62º F and an annual precipitation of only 37 millimeters. The amount of dust generated required the mine to use 11 water trucks operating 24 hours a day, 7 days a week, and there were plans to add an additional 3 trucks to keep up with the watering needs.
During Midwest’s initial observations of the site, we learned that 11 320-ton and 90 240-ton haul trucks operated at the mine site. The test section of roadway was part of a longer stretch of road between the mine and a dump site where these trucks would dump their loads. They traveled at 20 kilometers-per-hour loaded and 52 kilometers-per-hour unloaded.
The road surface itself was in decent overall condition, being lightly graded and watered prior to starting the dust suppressant applications. The road began with a flat section, went around a curve, then faced a slope. (This section of road was chosen because of the variability in surface types, from flat to curved to sloped, to test how EK35 would perform on each section.)
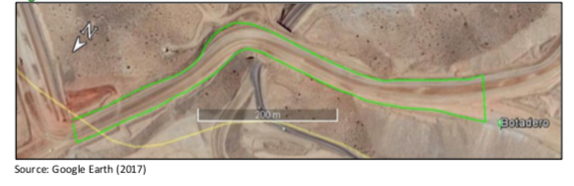
You can see these varying road types in the above image, highlighted within the green lines.
To quantify these different surface types, we broke the stretch of road into 6 zones. These next two images show how we identified these sections.
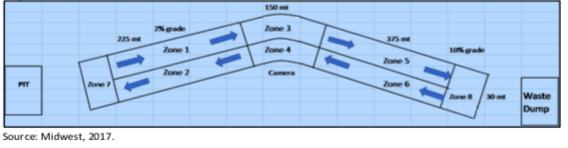
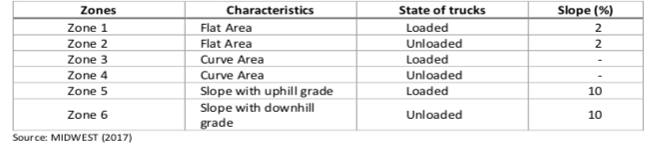
As you can see, each section of road has different characteristics that would impact the effectiveness of any attempts at dust control in mining. Slopes face different pressure than flat areas; lanes used by loaded trucks experience more weight; curves contribute to a more unstable road base.
Beyond the status of the road itself, Midwest also used trail cameras to evaluate and quantify the effectiveness of the current watering program. We found that watering was effective for up to 25 minutes, with dust plumes starting to form within 15 minutes. We conducted this observation on the flat area used by unloaded trucks, meaning this is where we would have expected to find watering having the greatest effect.
Areas of concern when approaching dust control in mining
During the pre-trial evaluation, 4 critical points were identified as potential sources of concern. These areas had characteristics that made them stand out from other road sections and individual application plans were needed to address these 4 areas. The areas of concern were:
- The loaded haul truck traffic coming from the pit operations were carrying dust onto the haul road trial section (zone 1 in the images above).
- At the transition point where the haul trucks changed gears to make the 10% grade (zone 5), there was spillage onto the road surface.
- The unloaded haul truck traffic coming from the waste dump operations were carrying dust onto the trial section (in zone 6).
- Loose material was present in the curve area (zones 3 and 4).
(Note: the carry-on dust described above has a significantly higher impact on the dust monitor readings on a trial section of only 750 meters than it would on a larger test section. Expanding the trial section would have reduced some of the challenges of this project, thereby improving the results.)
These 4 potential contamination sources were monitored. They had an impact on the frequency of applications in the sections adjacent to these areas. Controlling these contamination points was critical, as they would have a material impact on the trial results.
A final subject of concern that only emerged on the first day of the actual trial was that a new waste dump opened beside our trial section, increasing the truck volume from 100 vehicles per day to 300. The affect was to increase the spillage and carry-on issues mentioned above.
Objectives and final results
Going into this project, Midwest agreed on the following primary goals with the mine:
- Reduce watering by 80%-90%
- Reduce road grading by 50%-70%
- Determine the effectiveness of the current watering program
- Stabilize the road with EK35
To determine if these goals were accomplished, Midwest developed a systematic method for evaluating and quantifying the levels of dust generated by traffic. This method considers the height, length and duration of a given dust plume and places that dust plume into one of 4 categories. The following graphic and chart show how dust plumes are measured and grouped.
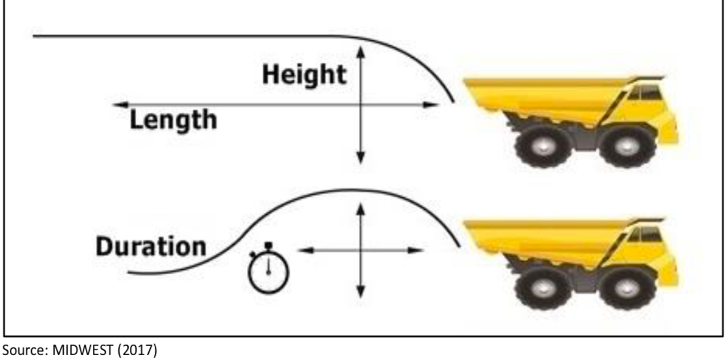
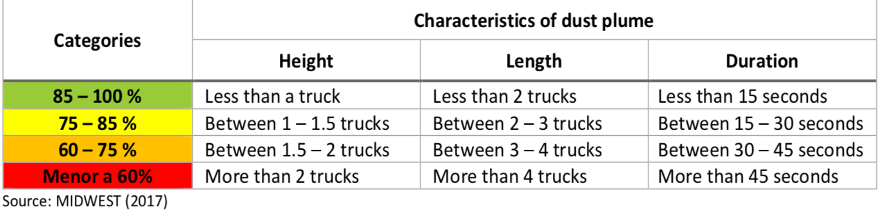
Midwest’s onsite personnel that were overseeing the trial used visual observations, discussions with operators and other onsite staff, photos, videos and test pits to help quantify the effect of applying EK35.
The results were very positive:
- EK35 successfully stabilized road surfaces on flat and uphill sections of the test area, despite traffic volumes that were 3 times the originally scoped amount
- Reduced watering by 80%
- Reduced grading by 50%
- Reduced dust by an average of 80%, compared to 30-40% from the watering program
- Achieved comparable costs to watering on flat and uphill sections, despite getting far better results (and longevity)
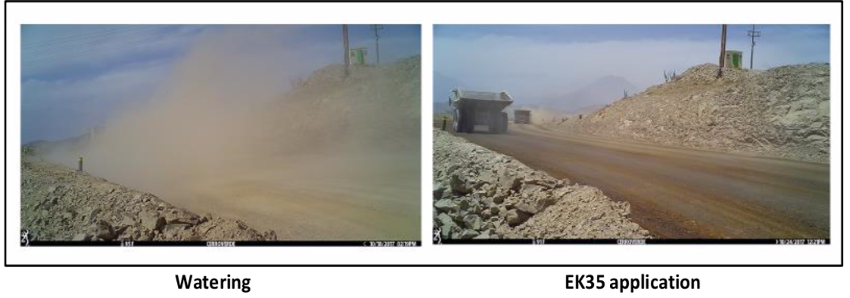
The challenges described in the above section came into play in zones 6, 3 and 4. Zone 6 was the downhill slope returning from the dump site. Because of the newly placed dump site, there was a high level of carry-on contamination that, combined with the high shear forces of haul trucks breaking while heading downhill, made getting accurate measurements of dust control difficult. Despite this, EK35 was deemed effective at creating a stabilized base layer and controlling dust on this zone as well as zone 5.
Zones 3 and 4 were the curved sections of the road. During the trial, it was observed that the surfaces of these zones were deteriorating and, by doing so, were generating dust. Midwest sought to stabilize these sections with a further application of EK35 mixed into the top 4-6 inches of road surface. This process did help stabilize the road surface, but it became clear that these sections would need to be completely rebuilt with a better quality road building material and receive a larger dose of EK35 in order to support the weight of the haul trucks.
This particular challenge helps showcase that dust control in mining is more complicated than just throwing down an off-the-shelf product (or excessive amounts of water). Different road conditions require different approaches to application. This is why we always say it’s about the entire program, not just the product. The program encompasses initial site evaluation, application expertise and oversight by experienced technicians and tracking and tweaking of the results to maximize effectiveness.
We only learned about the challenges facing the curved sections during the trial, and the results of the trial helped the mine have the accurate data needed to best determine the most appropriate course of action.
This level of evaluation, analysis and performance is available to any mine seeking to improve their dust control program to get the most cost-effective results possible. Contact Jim Silva (VP – Mining Business Unit) or Lynn Edwards (Senior Sales Manager) to see if a test is ideal to determine if there’s a more cost-effective way of controlling the dust produced by your mining operation.