By making a number of relatively minor infrastructure improvements, the MBTA can deliver faster and more reliable service to its riders.
The Massachusetts Bay Transportation Authority (MBTA) has had its fair share of challenges in recent years. Between an aging fleet of diesel locomotives to regular delays and slow service, public transit by rail in the Greater Boston area is struggling to provide riders with the fast and reliable transportation they depend on.
In recent years, the MBTA has proposed a number of ambitious plans to address these issues. One plan would include a multi-billion dollar expansion of Boston’s South Street Station while another would pave the way for additional double-decker passenger rail cars. However, the transit advocacy group TransitMatters has recently presented a proof of concept that identifies modest improvements that would greatly improve service across the MBTA network at a far lower cost.
Such improvements to the MBTA’s infrastructure represent a realistic way to improve service and reduce travel times. However, in addition to the changes proposed by TransitMatters, the MBTA should consider what rail maintenance products — such as anti-icing and deicing solutions — they can invest in to protect that infrastructure and ensure a smooth, uninterrupted experience for passengers.
The Current State of Affairs
The proof of concept from TransitMatters identifies key shortcomings across the MBTA network. By remedying the current unsatisfactory state of affairs, they argue that it’s possible to provide better transit outcomes without having to invest in multi-billion-dollar station expansions or purchasing a new fleet of bi-level coaches.
To name a few examples, MBTA commuters often need to use stairs to access trains at many stations; the current maximum speed along much of the line is just 60 miles per hour; the diesel locomotives that the network uses are inefficient and prone to breakdowns; and bi-level coaches make boarding and deboarding hectic and time-consuming. What’s more, service along much of the line is infrequent, causing passengers to overcrowd what trains are available.
Potential Improvements to Boston’s Rail Infrastructure
To fix these issues and improve service, TransitMatters has recommended several relatively straightforward improvements that the MTBA could make. For starters, adding higher-level platforms could cut down on dwell times and make the trains more accessible for all passengers. Additionally, upgraded tracks can be made to support top speeds of 90 — or even 100 — miles per hour along the straightest sections.
Additionally, the MBTA’s diesel locomotives could be phased out in favor of electric trains. While the former experience breakdowns every 5,000 to 25,000 miles, electric trains break down every 455,000 miles on average. Finally, more frequent service — every hour or half-hour along each line — could cut down on congestion across the region and eliminate the need for new bi-level coaches.
Delivering Better Service for Riders
For MBTA stakeholders, surging ridership and aging infrastructure call for renewed investment in the passenger experience. However, in addition to considering the changes proposed by TransitMatters, the MBTA should evaluate how they can best protect and maintain their passenger rail network over time.
With anti-icing and deicing solutions from Midwest Industrial Supply, Inc., it’s possible for the MBTA to deliver fast and reliable service for its passengers — regardless of the weather conditions that often plague the American Northeast. Our Zero Gravity anti-icers and deicers — co-developed by NASA and Midwest — provide a long-term, non-freezable solution that can keep passenger rail running regardless of snow or ice. By investing in proven products built by Midwest experts, rail operators can put their passengers first.
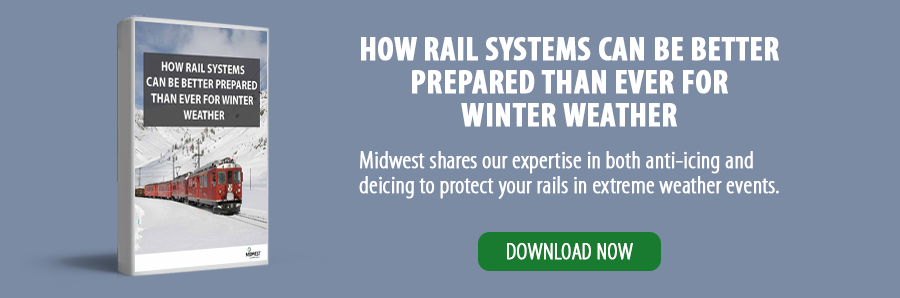