With AI technology scaling rapidly across practically all industries, steel producers in particular should be ready to leverage its unique benefits across operations systems and critical infrastructure.
Steel production is a uniquely competitive market. Steel is simultaneously the most in-demand metal in use today and one of the most widely produced as companies strive to meet that demand. This means that the pressure is on steel producers to make their operations as efficient as possible in order to cut down on overhead and offer customers the most competitively priced, high-quality products available.
To do so, steel producers should be looking to leverage the latest and greatest technology to streamline their facilities and support critical infrastructure. Artificial intelligence (AI) is an indispensable tool for exactly this type of use case, offering the steel industry the kind of data-driven insights necessary to deliver a better product at a lower cost for them and their customers.
While steel producers consider how they can best leverage the strategic benefits of AI for their operations, they should also be considering what else they can do to prepare their infrastructure for the future. For example, ensuring that access roads are properly maintained and structurally sound is a critical investment for steel producers. With the right dust control products in hand, you can ensure you’re protecting this infrastructure and cutting down the levels of airborne dust your workers are exposed to.
Digital Twins
To truly benefit from AI technology, steel producers should be investing in something called digital twins. A digital twin is a virtualized version of any industrial process and provides much-needed insight into the ongoing functionality of critical machinery, supply chain operations, and key checkpoints throughout the production process. Digital twins can even be set up for products that have already been delivered to customers and are currently in use.
By setting up a digital twin for these different stages of steel production, enterprises can link their physical equipment with their digital environment — and doing so yields a wide range of important benefits. For example, steel producers can capture a wealth of information from every stage of the production process; they can monitor the performance of their products once customers are using them; and they can improve the flow of information among supply chain stakeholders by boosting data visibility.
Big Data Analytics
Once steel producers have merged their physical operations with their digital environment, they can begin thinking about how to use that data. Best practice dictates that companies then set up something called data lakes — single repositories that hold all of the information gathered from digital twins, Internet of Things technology, and more. That treasure trove of raw data can then be fed through advanced analytics, machine learning, and AI systems to produce actionable business insights for decision-makers at all levels of a given organization.
By using AI to interpret this data and glean actionable insights, enterprises can make good on their investments in data infrastructure. They’ll be able to better understand market trends to predict price fluctuations, analyze factory data to optimize capacity and monitor equipment health, track business information, and better communicate with supply chain partners and customers.
Finding Efficiencies and Improving Productivity
For steel producers determined to improve day-to-day operations and streamline their business processes, AI is an essential part of the modern enterprise tech stack. By collecting data from across multiple physical environments and then leveraging it to yield critical insights, businesses can cut unnecessary costs and pass on the savings to their customers.
However, it’s equally important that steel producers invest in the physical infrastructure of their worksites if they expect to fully reap AI’s rewards. By investing in Midwest Industrial Supply, Inc.’s proven dust control products and managed service programs, for example, enterprises can protect and maintain the access roads that are so important to maintaining efficient operations and reducing airborne dust.
Midwest has more than 40 years of experience designing custom dust control solutions and application strategies for industrial enterprises. Leveraging our patented suite of synthetic organic dust control products, we can improve the strength of your roads while significantly reducing ongoing maintenance costs.
Whether you’re looking for a turnkey dust control solution or a product that you can apply on your own, reach out to the team at Midwest for answers.
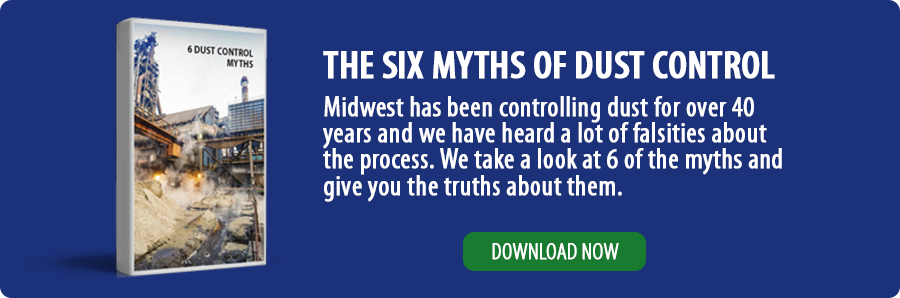